The Ontario Court of Justice has recently set new fines for many sectors, check out the new fines for the industrial sector as well. The Ministry Of Labour inspectors are given the authority to issue tickets for violations against the Occupational Health and Safety Act (OHSA). These tickets are usually a low dollar value fines meant to provide a a stronger message against companies that fail to comply with safety laws. Usually, a Ministry of Labour (MOL) ticket will also require the employer to follow up with an inspector to make sure that they have since complied all OHSA regulations. Failure to comply or follow up with the MOL inspector can result in further monetary charges.
Call us at 1800-219-8660 or leave a us a message if you need more information or if you need help with complying with the Occupational Health and Safety Act. Check out our safety training courses!
Below you will find the latest fines set by the Ontario Court of Justice for the industrial sector:
Schedule 67.1
Ontario Regulation 213/91 under the Occupational Health and Safety Act
Item | Offence | Section | Set Fine | Previous Set Fine |
1. | Constructor failing to notify Ministry of Labour of construction project | 6 (3)–(5) | $550 | New |
2. | Constructor failing to notify Ministry of Labour of work on a trench | 7 | $550 | New |
3. | Constructor failing to notify Ministry of Labour of use of suspended work platform system | 7.1 (2) and (4) | $550 | New |
4. | Constructor failing to appoint supervisor for project with five or more workers | 14 (1) | $550 | New |
5. | Constructor appointed supervisor failing to supervise work at all times | 14 (2) | $550 | New |
6. | Employer failing to appoint supervisor for five or more workers on project | 15 (1) | $550 | New |
7. | Employer appointed supervisor failing to supervise work at all times | 15 (2) | $550 | New |
8. | Constructor failing to establish written emergency procedures | 17 (1) | $550 | New |
9. | Constructor failing to post emergency procedures | 17 (3) | $550 | New |
10. | Worker failing to wear protective headwear | 22 | $250 | New |
11. | Worker failing to wear protective footwear | 23 | $250 | New |
12. | Worker failing to wear eye protection | 24 | $250 | New |
13. | Employer failing to ensure training on fall protection | 26.2 (1) | $550 | New |
14. | Employer failing to ensure that written training and instruction record is prepared | 26.2 (2) | $550 | New |
15. | Employer failing to make training and instruction record available to inspector | 26.2 (4) | $550 | New |
16. | Constructor failing to ensure clean-up or toilet facilities available | 29 (3) (a) | $550 | New |
17. | Constructor failing to ensure required access to facilities | 29 (4)–(7) | $550 | New |
18. | Worker failing to use provided respiratory protective equipment | 46 (2) | $250 | New |
19. | Employer failing to develop written traffic protection plan for workers exposed to hazard from vehicular traffic | 67 (4) and (5) | $650 | New |
20. | Worker directing vehicular traffic for multiple lanes in the same direction | 69 (2) | $250 | New |
21. | Worker who may be endangered by vehicular traffic failing to wear prescribed garment | 69.1 | $250 | New |
22. | Worker inappropriately standing or stepping on ladder | 83 (2) | $250 | New |
23. | Operator leaving controls of the machine unattended | 102 | $250 | New |
24. | Worker passing shovel, backhoe or similar excavating machine or its load over a worker | 103 (1) | $250 | New |
25. | Worker passing crane or similar hoisting device’s load over another worker | 103 (2) | $250 | New |
26. | Worker doing other work while acting as signaller | 106 (1) | $250 | New |
27. | Signaller failing to wear prescribed garment | 106 (1.1)–(1.4) | $250 | New |
28. | Worker using as a work place an object capable of moving supported by fork-lift truck, front-end loader or similar machine | 107 | $250 | New |
29. | Worker failing to wear adequate personal protective equipment and clothing while using chain-saw | 112 (1.2) (a) | $250 | New |
30. | Worker failing to wear adequate eye and hearing protection while using chain-saw | 112 (1.2) (b) | $250 | New |
31. | Worker failing to wear adequate personal protective equipment while using fastening tool | 117 (3) (a) | $250 | New |
32. | Worker failing to wear adequate eye protection while using fastening tool | 117 (3) (b) | $250 | New |
33. | Employer failing to ensure that worker using suspended work platform system or boatswain’s chair is trained | 138 (1) and (2) | $550 | New |
34. | Employer failing to ensure that competent worker is trained | 138.1 (2)
and (3) |
$550 | New |
35. | Owner failing to ensure there is an adequate roof plan | 141.2 (1) | $550 | New |
36. | Worker failing to wear full body harness connected to fall arrest system while on or getting on or off suspended work platform or boatswain’s chair | 142.06 (1) | $350 | New |
37. | Constructor failing to notify Ministry of Labour of multi-point suspended work platform | 142.3 (1) | $550 | New |
38. | Worker without prescribed qualifications operating crane or similar hoisting device | 150 (1) | $250 | New |
39. | Worker without prescribed qualifications operating a crane or similar hoisting device | 150 (2) | $250 | New |
40. | Employer failing to ensure that qualified worker operates a rotary foundation drill rig | 156.6 (1) | $550 | New |
41. | Worker operating a rotary foundation drill rig without the prescribed training or qualifications | 156.7 | $250 | New |
42. | Worker without prescribed qualifications connecting, maintaining or modifying electrical equipment or installations | 182 (1) | $250 | New |
43. | Constructor failing to establish and implement written measures and procedures | 188 (4) (a) and 188 (5) | $550 | New |
44. | Constructor failing to make written measures and procedures available to every employer on project | 188 (4) (b) | $550 | New |
45. | Employer failing to provide copy of written measures and procedures to a worker | 188 (6) | $550 | New |
46. | Employer failing to mark gas, electrical or other services before excavating | 228 (1) (a) | $650 | New |
47. | Employer failing to ensure that services are accurately located and marked before excavating | 228 (1) (b) | $550 | New |
48. | Worker failing to ensure that services are accurately located and marked before excavating | 228 (1) (b) | $250 | New |
49. | Constructor failing to take precautions to prevent damage to adjacent building or structure | 229 (1)–(3) | $550 | New |
50. | Worker operating machine so as to affect excavation wall stability | 233 (3) | $250 | New |
51. | Worker positioning machine so as to effect excavation wall stability | 233 (3) | $250 | New |
52. | Constructor failing to keep support system design drawings and specifications at project | 236 (7) | $550 | New |
53. | Employer failing to notify Director before working on tunnel, shaft, caisson or cofferdam | 245 (1) | $550 | New |
This could be interpreted as companies only needing to train their workers to wear a harness and to know how to inspect one when it comes to working at heights. The Ministry of Labour did not seem keen to define exactly the training parameters needed to train workers effectively in this scenario.
The proposal also addressed the need for businesses to conduct risk assessments for work that could be considered ‘high risk’. What the MOL is asking businesses to do is:
- Conduct a risk assessment of jobs that have associated safety risks.
- Once the risks have been identified, and this would include working at heights risks (ladders, scissor lifts, cages, scaffolds, etc.), develop some means of control to protect your workers. The risk assessment controls matrix determines that you should first try to eliminate the risk, and if you can’t, minimize it by implementing safe work instructions or the use of personal protective equipment such as safety harnesses and lanyards.
- Train workers on the hazards associated with the work they are tasked. This training may include the proper use of any personal protective equipment (PPE).
What is the future of Working at Heights for the Industrial Sector?
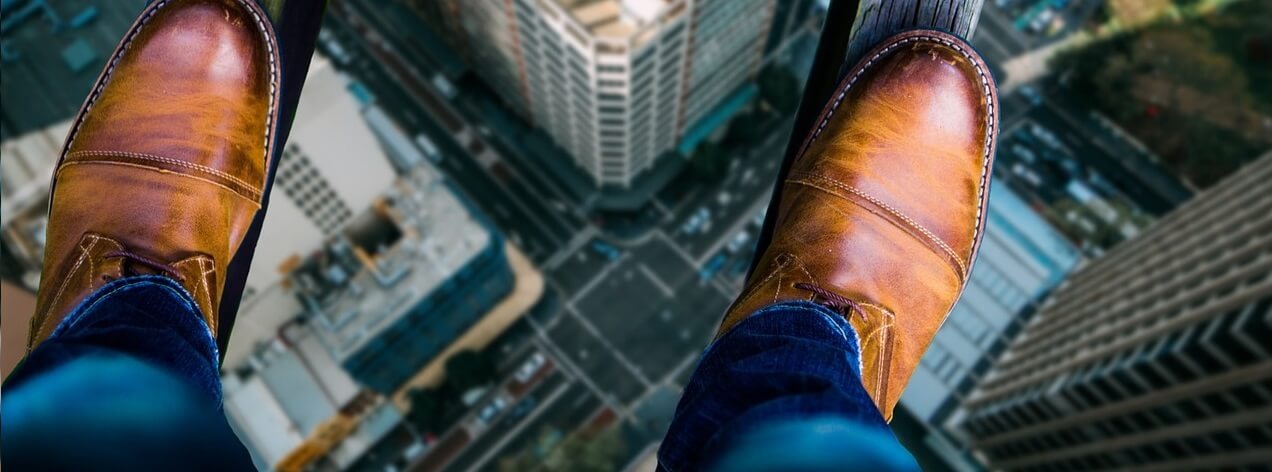
For now, it appears that businesses will need to create risk assessments that are documented and shared with the company’s Joint Health & Safety Committee. Risk assessments will lead to writing safe work instructions, allowing your workers to know the clear guidelines your company wants to uphold in order to minimize hazardous conditions. These safe work instructions will have to include working at heights as well. For example, if the work involves using ladders, you would have to include elements on the proper use of said ladder. Not only would the instructions be about the basic rules of ladder safety, but also what exact ladder is to be used and how to set it up properly. If your company were to use equipment such as scissor lifts or working on scaffolds, your safe work instructions would have to include the proper use of safety harnesses and lanyards. As with ladders, you would also provide specific instructions on what type of harness and lanyard workers need to use, and how to be tied off properly and to what anchor point.
We assume the Ministry of Labour decided to only propose these changes because of the difference in industrial and construction sectors. In construction projects, every day could be potentially different since they could be working in multiple sites with different conditions, different anchor points, etc. Workers in construction are taught to evaluate the work they will be conducting and the different ways they could protect themselves from a potential hazard. Industrial projects, however, have rules and processes in place which makes the work more consistent. Industrial businesses have the ability to determine where their workers could be at risk and be much more specific as to how workers can ensure their safety.
We believe the Ministry of Labour’s plan is to have companies train their own workers with their own tools and equipment. In a near future, you may choose not to use a company like Industrial Safety Trainers anymore for Fall Arrest/ Fall Protection training and instead use us for risk assessments and consulting. We will be able to help you with your risk assessment, teaching you how to create safe work instructions, and how to train your own workers properly. The actual training for working at heights for industrial establishments may have to fall on the company’s hands.
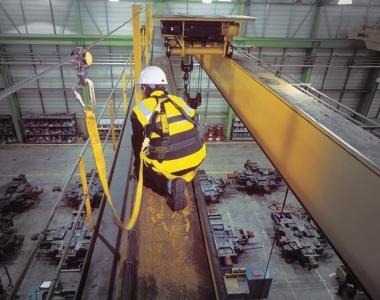